The Svaja Story.
Excellence Speaks For Itself
Svaja takes its name from the founder Kristina Svajone Bobs, for her name in her native Lithuania, means ‘dream’. Kristina’s dream was that of creating and developing collections of usable, beautiful art in whatever medium.
From Svaja’s beginnings in 1999, Kristina has driven her company forward with a proven flare for designing glass that is celebrated across the world.
Over the years Svaja has completed many prestigious projects for clients across the globe; from prominent luxury hotels and resorts to corporate headquarters. Svaja products can be seen in world class restaurants, fine boutiques, fashion and homes stores and exquisite private residences around the world.
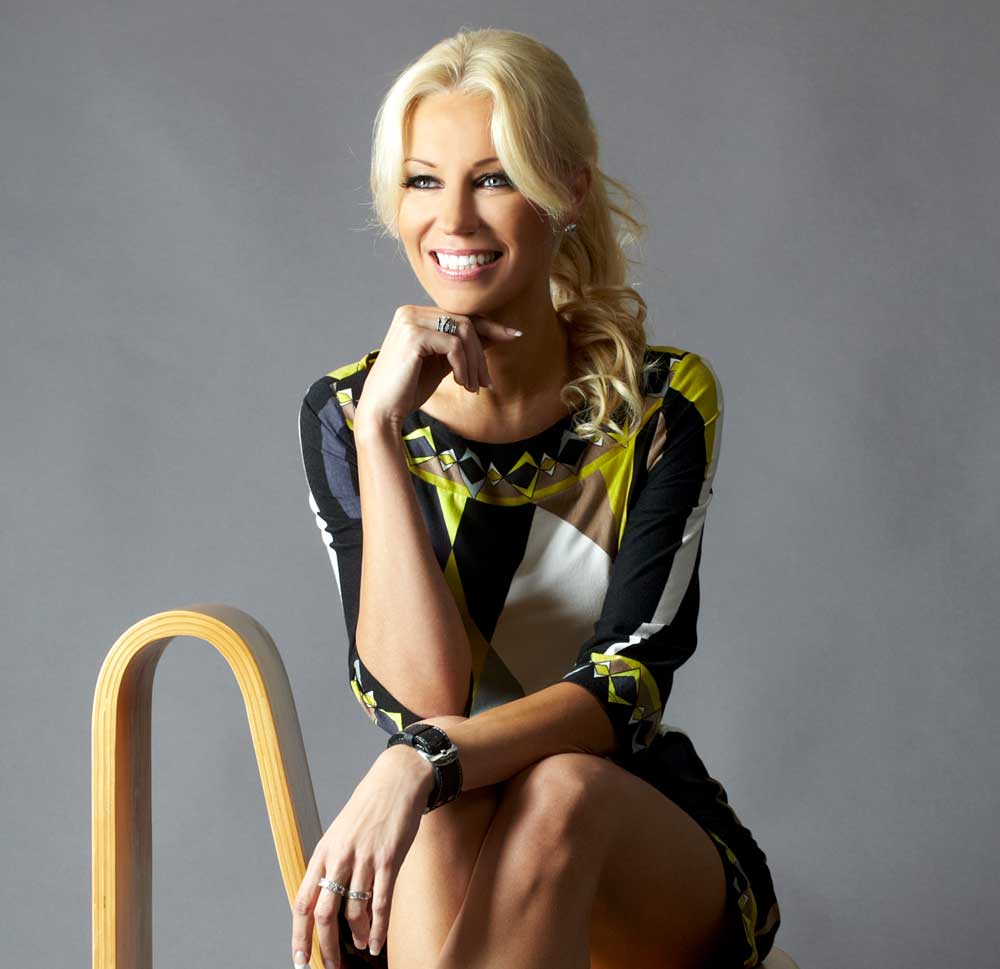